The Ultimate Checklist for Successful Mixer Loading and Extruder Feeding Systems
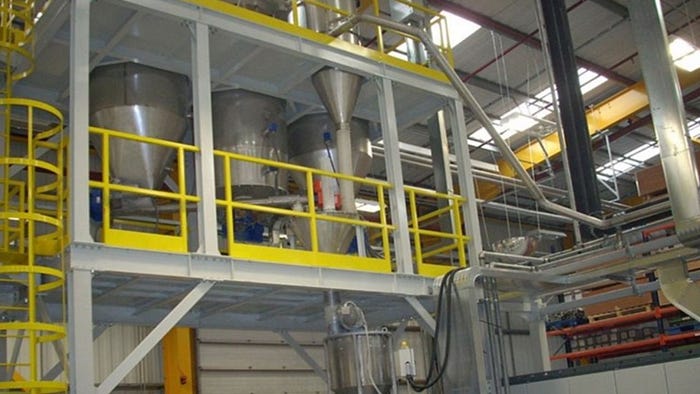
In the ever-evolving world of industrial manufacturing, the quest for operational excellence is a constant pursuit. Dermakmixer, a prominent player in the Turkish manufacturing landscape, has emerged as a leader in providing innovative solutions for mixer loading and extruder feeding systems. The key to a seamless and efficient production process lies in adhering to a comprehensive checklist. This article aims to explore the ultimate checklist for ensuring the success of mixer loading and extruder feeding systems at Dermakmixer in Turkey.
Equipment Inspection and Maintenance:
One of the foundational pillars of a successful manufacturing operation is the regular inspection and maintenance of equipment. Mixer loading and extruder Feeding Systems at Dermakmixer require meticulous attention to detail. Regularly inspecting components such as belts, hoppers, and conveyors ensures that they are in optimal condition. Scheduled maintenance prevents unexpected breakdowns and extends the lifespan of the machinery, contributing to long-term operational efficiency.
Material Quality Control:
The quality of raw materials directly impacts the consistency and performance of the final product. Dermakmixer places a premium on using high-quality materials. Implementing stringent quality control measures to verify material properties before loading into mixers and extruders is crucial. Regular testing and analysis of materials ensure that the integrity of the final product is maintained, meeting the highest standards of quality.
Precision in Mixing Ratios:
Achieving the desired product specifications hinges on establishing and adhering to precise mixing ratios. Dermakmixer employs advanced controls and automation systems to ensure accuracy in mixing processes. Regular calibration of equipment is paramount to maintaining consistent mixing ratios, contributing to the production of high-quality and uniform products.
Dust Control Measures:
Dust control is a critical aspect of maintaining a safe and clean working environment. Dermakmixer prioritizes the implementation of effective dust control measures during mixer loading and extrusion processes. The installation of dust collection systems minimizes airborne particles, ensuring a healthier workplace. Proper training of personnel on the handling and disposal of dust-related byproducts further contributes to a safer and more sustainable production environment.
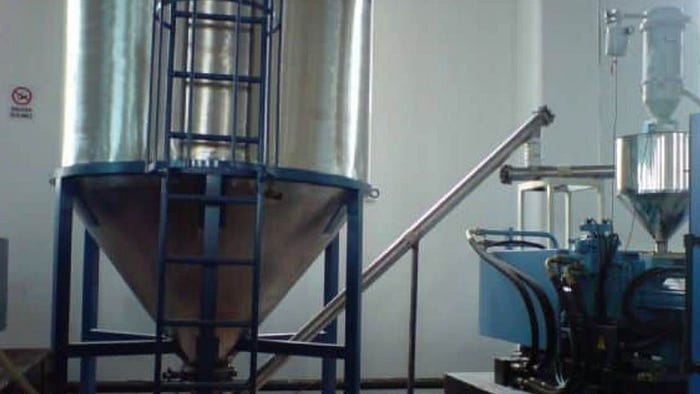
Automation and Monitoring Systems:
In the era of Industry 4.0, automation and monitoring systems play a pivotal role in ensuring operational efficiency. Dermakmixer invests in state-of-the-art Automation systems for real-time monitoring of mixer loading and extruder feeding processes. The integration of sensors and feedback mechanisms allows for the prompt detection and correction of any deviations in the production process. Smart technologies, including data analytics, provide valuable insights for optimizing operational efficiency.
Operator Training and Safety Protocols:
Human capital is a critical asset in any manufacturing operation. Dermakmixer recognizes the importance of providing comprehensive training programs for operators. Enhancing their skills in managing mixer loading and extruder feeding systems not only improves efficiency but also contributes to a safer working environment. Emphasizing and enforcing safety protocols minimizes the risk of accidents, ensuring the well-being of the workforce.
Energy Efficiency Considerations:
In an era where sustainable practices are gaining prominence, Dermakmixer explores energy-efficient technologies for mixer loading and extrusion processes. Optimizing equipment settings and configurations to minimize energy consumption aligns with the company’s commitment to environmental responsibility. Embracing sustainable practices not only reduces the environmental impact but also positions Dermakmixer as a forward-thinking and responsible industry leader.
Regulatory Compliance:
Adhering to industry regulations and standards is non-negotiable for Dermakmixer. Staying informed about and compliant with local and international quality and safety standards is an ongoing commitment. Regular audits are conducted to ensure that the company operates within the parameters set by regulatory bodies, reinforcing Dermakmixer’s reputation for delivering products of the highest quality and safety standards.
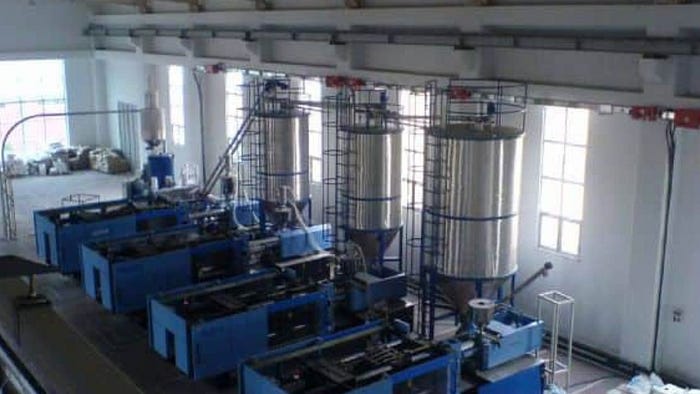
Conclusion:
In the competitive landscape of industrial manufacturing in Turkey, Dermakmixer stands as a testament to innovation and excellence in mixer loading and extruder feeding systems. By diligently following the ultimate checklist outlined above, businesses can ensure the success of their operations, achieving efficiency, consistency, and safety in every stage of the production process. As technology continues to evolve, staying committed to continuous improvement and innovation will be key to maintaining Dermakmixer’s leadership position in the industry and contributing to the overall advancement of Turkish manufacturing.
Comments
Post a Comment