How to Choose the Right Loading and Extruder Feeding System?

For any plastics extrusion operation, having the right loading and feeding system is critical for consistent production, quality, and efficiency. The feeding system controls the rate at which raw material is delivered into the extruder barrel for melting and extrusion. An improper feeding system can lead to issues like inconsistent extrudate properties, surging, excessive material waste, and even equipment damage.
With the variety of loading and feeding solutions on the market, how do you determine the ideal setup for your application? Here are some key factors to consider when choosing a loading and extruder feeding system:
Material Characteristics
The first major consideration is the type of raw material being used. Plastics come in many different forms — pellets, powders, regrinds, liquids, etc. The bulk density, particle size, flowability, and melting properties will influence the optimal feeding system design. For example, lighter, fluffier materials often require a specialized vacuum or force-feeding system.
Throughput Rate
You’ll need to match the feeding system’s rated throughput capacity to the desired extruder output rate. For higher extruder rates, a high-capacity grizzly or upstroke feeder may be needed rather than a standard volumetric or gravimetric feeder. Simultaneously feeding multiple components, additives, or regrind streams also impacts the required throughput.
Accuracy Requirements
Some processes, like compounding, demand a very high degree of precision and consistency in the material feed rate to maintain tight tolerances. In these cases, investing in an advanced gravimetric batch or loss-in-weight feeding system is worthwhile despite the higher costs. Less critical extrusion runs may allow for simpler volumetric feeders.
Extruder Barrel Diameter
Pay attention to the throat size of the extruder in relation to the feeders discharge outlet size. Having a hopper or feeding inlet that is too narrow can cause bridging or material flow disruption. A feeding system matched to the extruder throat avoids this constraint.
Automation Integration
For modern extrusion plants, it’s crucial that the feeding system can seamlessly integrate with other automation platforms, PLCs, and control systems on the line. This allows for recipe-driven automated control over feed rates and ratios for changeovers and data collection. Open connectivity also enables options like remote monitoring.
Flexibility and Adaptability
If you extrude a wide variety of materials, parts, or products, a flexible feeding system that can handle different setups is valuable. Look for hoppers and bins with quick-swap capabilities, along with easily adjusted feeding tubes and hoppers. Mobile or portable feeders offer even greater flexibility.
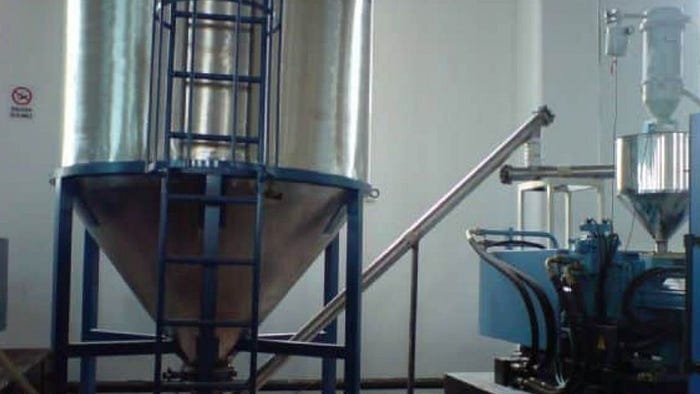
Safety and Cleanability
Don’t overlook important safety considerations like enclosed designs to contain dust or pellet leaks. Feeders with hinged frames, slide gates, and other access points allow for easier cleaning between runs. Specialty coatings and finishes prevent material hang-ups.
Space Constraints
Loading and feeding systems need to fit appropriately into the available plant floor space and footprint around the extruder. Vertical, tower feeders provide a smaller footprint, while larger reservoir hoppers require more clearance area.
By carefully evaluating your process needs and plant’s operational requirements, you can select a loading and extruder feeding setup that ensures optimal performance. Work with an experienced manufacturer that can guide you through the selection and system integration process.
Comments
Post a Comment